Our Software
EXAKT: Condition-based Optimization Software
EXAKT FACT SHEET
To Order
Introducing EXAKT into Your Operation.
What’s Involved?
EXAKT, a development of the Centre for Maintenance Optimization
and Reliability Engineering (C-MORE) at the University of Toronto,
is finding acceptance in the commercial world as an answer to
obtaining reliable predictions of failure in machine parts and
assemblies.
EXAKT collaborations through C-MORE have taken place with
Syncrude, Irving Pulp and Paper, U.K. Ministry of Defence, Zachry
Construction, Teck Resources, TransCanada Pipelines, EDF (French
nuclear power generation), Hydro One Networks, and XEROX.
This webpage is designed to provide, to enquirers, the answers to
a number of typical questions related to the implementation of
EXAKT. We think it will succeed in that regard, but we also invite
you to contact us further for any additional information you’d like
to have.
A Typical Company Situation
Many organizations undertake extensive condition monitoring of their fixed
and mobile assets. With the wealth of data being captured they may wish
to test the role of condition based maintenance software (EXAKT) to
optimize their maintenance decision-making.
Organizations often wish to analyze data from condition monitoring data
acquisition systems such that they can take optimal hazard/cost decisions.
EXAKT can be used to define which co-variates (key risk factors, i.e.,
measurements) are important to measure on line by these condition
monitoring (CM) systems to detect impeding failure from various failure
modes.
To compliment the insights that can be obtained from an organization’s
condition monitoring measurement system they often wish to enhance
maintenance decision making through proactively using this data in the
EXAKT software to optimize equipment performance — such as through
maximizing equipment availability or minimizing total cost.
To achieve this data is extracted from the condition monitoring databases,
to be combined with work order data (usually contained in a computerized
maintenance management system (CMMS)) to perform various conditionbased
maintenance analyses in EXAKT.
A Common Approach to Using EXAKT
Information Regarding Extraction of Condition Monitoring Data for
Fixed and Mobile Assets.
This document provides a high-level summary of what should be extracted
from the condition monitoring databases, to be combined with work order
data to perform various condition-based maintenance analyses in EXAKT.
It is not possible at this stage to advise on exactly which signals to extract. Any signal plausibly related to equipment failure can be extracted. It is better to initially extract too many signals than to extract too few and miss
a key risk factor by accident.
The extracted data will consist of a list of records. Each record will be
identified by a unique equipment ID, the record date, the working age of
the equipment, and any number of condition-monitoring readings recorded
at that moment.
The following sections provide information on these topics:
-
EXAKT implementation including process flow, implementation
time, implementation requirements, and documentation
- Regarding KPI for effectiveness of EXAKT outputs
EXAKT Implementation
A high-level description of the basic required inputs and possible results is
summarized in the following diagram:

An EXAKT implementation consists of the selection of a fleet of similar
units to analyze, the processing and analysis of data associated with the
fleet, the development of appropriate models, any IT modifications
required to corporate databases with EXAKT installations, and all training
and support on software use and interpretations. The selection of a new
fleet of equipment constitutes a new implementation, with possibly much
lower IT and training requirements.
EXAKT consists of two modules: EXAKTm for modeling, and EXAKTd for
decisions. EXAKTm contains routines for data analysis, assessment,
correction, and modeling, and requires substantial training and experience
to use. EXAKTd is used to produce outputs such as remaining useful life
and optimal maintenance decisions using an established model and the
latest available data, and requires a smaller amount of training to use.
The following is the process flow of an EXAKT implementation:
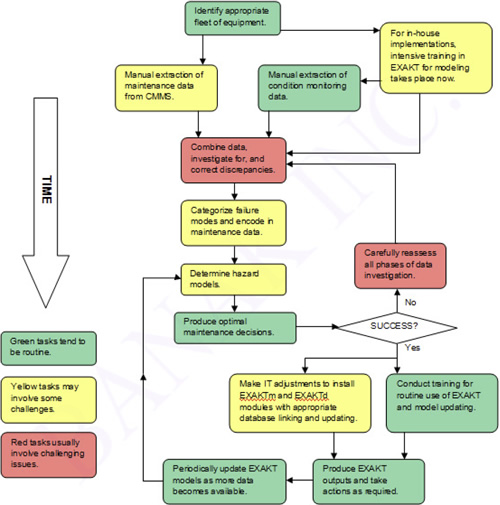
An appropriate equipment fleet must be selected. The equipment must
have historical data available on installations and removals of components,
and this equipment should have been subjected to condition monitoring
(CM).
The initial analysis is conducted on data extracted from CM and CMMS
databases. The extraction of CM data is usually more straightforward than
the extraction of CMMS databases, as the latter database depends more
on human intervention than the former.
Data from these sources are combined and assessed for errors and
discrepancies. This is the phase of analysis that can be the most difficult
and time consuming, depending entirely on the quality of the input data.
Next, an assessment of the failure modes must take place. Similar failure
modes should be identified to be analyzed together, and the probably
relationships between CM data and failure modes should be established.
Once the data are suitably cleaned, hazard modeling can take place. This
process can be straightforward unless the CM data contains a very large
number of variables or the relationship between CM data and failures is
somehow complex. A suitable hazard model is identified for a particular
failure mode. This model will provide the key covariates correlated to
failure and an estimate of any ageing effect remaining after the covariates
have been accounted for. Then:
- EXAKT will model how the covariates change in time.
- Using the hazard model, the covariate change model, and information
relating to the cost of failure and the cost of performing preventive
maintenance, EXAKT can compute the optimal maintenance policy, as
described in points 3 to 5 below.
- A maintenance policy is defined as: the hazard rate level at which a
preventive removal should occur. The optimal maintenance policy is
one that achieves the best balance of failures allowed to occur and
preventive removals, where “best” depends on the desired criteria.
Two common criteria are: minimizing total cost, and maximizing
availability.
- The expected total cost (or maximum availability) resulting from a
particular hazard rate level that defines a maintenance policy is
computed by EXAKT. An example plot of costs associated with various
hazard levels is:
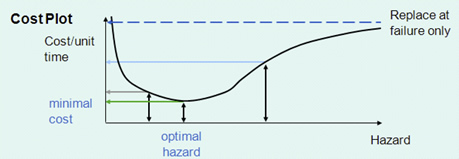
-
The optimal hazard rate is identified by the minimum cost. This optimal hazard rate
defines the optimal maintenance policy. In EXAKT, the optimal maintenance policy is
displayed in an easy to use decision chart that incorporates the key covariates, the
age of the equipment, and the cost information, as illustrated in the following
example:
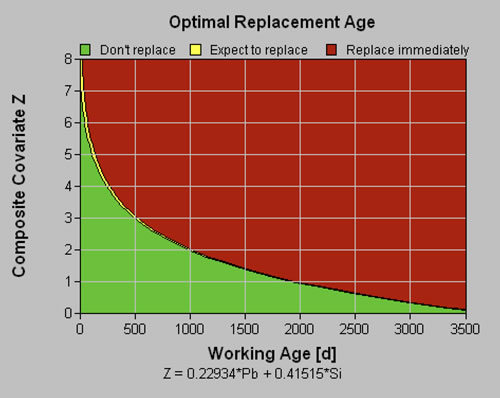
When updated values for the key covariates (in this case, lead and silicon)
become available, EXAKT will plot the point corresponding to the age of
the equipment and the weighted values of the covariates. If the point
lands in the green zone, it is not yet time to perform preventive
maintenance. If the point lands in the red zone, it is time to perform
preventive maintenance. (If the point lands in the yellow zone, it may be
time to replace before the next inspection occurs.)
It cannot be guaranteed that there will be useful predictions from data
analyzed using EXAKT in a particular case. The lack of a suitable model
can result from any subset of the following causes:
- the CM data is simply a poor predictor of the failures.
- one or more data sources was of very poor quality or otherwise
insufficient.
-
one or more data sources was not properly assessed before modeling
took place.
A careful reassessment of the date would have to take place to determine
the next course of action, which may involve more modeling or a selection
of a different equipment fleet.
When suitable models have been identified, technicians and engineers
need to receive some training (see section Error! Reference source not
found. below) on the routine use of
EXAKT, including how to periodically update models when enough new
data become available.
At the same time, any IT installations and modifications should take place
in preparation for a full implementation. The EXAKTd module for decisions
should be installed on any computer used by engineers and technicians
needing access to EXAKT outputs. The EXAKTm modeling module should be installed on computers where model updating will take place.
EXAKT can read data from any ODBC source, so in principle it can be easy to set
up the required data connections, with perhaps some straightforward SQL
programming required. BANAK would undertake the programming details
within EXAKT. The details of a site’s IT infrastructure can result in the
following challenges:
- database security may make it inconvenient or impossible to set up
simple ODBC connections from any EXAKT installation to the data,
requiring more programming work to extract data securely. This work
can be handled by BANAK.
- in such cases extra programming work may be required of the CMMS
or CM database OEM, which could result in the need for intellectual
property agreements or amendments. These agreements or
amendments could be handled by BANAK.
1. Possible Condition Monitoring Data
The only limitation on what can be used as a condition-monitoring (CM) variable is
that it has the possibility to be expressed as a number. Most CM data is already
recorded numerically. Some categorical or descriptive data would have to be coded
is dummy (0-1) variables. It might prove challenging to translate free-form text
comments fields into a numerical format. Raw vibration signals typically require preprocessing
before being used in EXAKT.
Some CM data might be considered as measures of working age rather than true CM
readings. For example, fuel consumption rate is normally under control of the
operator who chooses the rate at which to do work.
In theory there is no limit to the number of records being analyzed; however,
computation speed may become slow on extremely large datasets (hundreds of
thousands of records). CM data recorded by sensors in near real-time can result in
datasets that are too large to be practically analyzed. In such cases some
engineering knowledge should be applied to the processing of these readings before
analysis within EXAKT. For example, if a common failure mode of interest is thought
to be preceded by a gradual loss in oil pressure, then an average oil pressure
reading over, say, one hour might be used, rather than a near-real time reading
resulting in thousands of largely redundant second-by-second readings.
Some initial processing of near-real time data would be done outside of EXAKT using
any suitable general purpose software.
EXAKT is usually best suited as a maintenance planning tool, and not a real-time
monitor of failures with very rapid onset. For example, a rapid decrease in some
pressure reading followed by a failure only a few seconds later may be difficult to
model in EXAKT, because EXAKT builds models relating CM measurements with
maintenance records. Maintenance records tend not to be accurate down to the
second. EXAKT cannot provide models that are more precise than the data used to
build them. Certainly, once EXAKT has determined a good model, it can then be
used in conjunction with online monitoring.
2. What Should Be Extracted Initially from CM Databases
EXAKT works by combining data from multiple sources. So it is essential that units
be identified in the same way from each source. It is also essential that each source record unit’s working age in the same manner. If this is not the case, some
modifications of the data must take place outside of EXAKT.
Data should be extracted into a standalone database first, for some processing
before being used by EXAKT. (Once models are constructed EXAKT can simply
access the raw data directly – by this time it will have been determined precisely
how EXAKT will be using the data.)
We call the unique identifier of a piece of equipment the Ident. The date on which
any reading or maintenance action takes place is the Date. The working age of the
unit is called the WorkingAge.
The raw data may contain other fields which may assist in the identification of units
and can help in ensuring data from different sources of data are combined correctly,
even if they are eventually not used by EXAKT. At this point it is always better to
keep more data rather than less. Call these miscellaneous identifiers Id1, Id2,….Finally there will be the CM readings themselves. They can be any reading that is (or
can be expressed) as a number and is plausibly related to the health of the
equipment. Call the CM readings at any particular time cm1, cm2, cm3,….
Then a typical record will look like this:
Ident Date WorkingAge Id1 Id2 … cm1 cm2 cm3…
The first row would contain suitable headings, ideally with the first three
called “Ident”, “Date” , and “WorkingAge”, but this is not necessary at this
point. The other headings should be short but informative and contain only
numbers and letters, if possible and convenient. But everything can be
changed if necessary.
IMPORTANT NOTES:
- Essentially: there is no reason to limit the number of signals to extract,
unless there are some clearly irrelevant ones. The "width" of a dataset is
not a problem. The length can be a problem with process data (near realtime)
and would have to be addressed outside EXAKT if necessary, as
EXAKT isn't suited to millions of records.
- The biggest problem is likely to come from aligning the data from the
CM data base and the CMMS.
- There is a possibility that no good EXAKT model can be found. For
example, in a recent study it was found that oil sampling gave no useful
prediction of part failures. The company representative subsequently
wrote: “The conclusion looks like being that we are wasting our time doing
oil analysis as it doesn't seem to reliably catch any failures, not even those
that are attributed to it.
I believe that this aspect of EXAKT, helping you not do activities that add
no value is under-rated as in “my organization” we do lots of activities just
because we have always done them, not because they add value.”
KPIs for assessing EXAKT performance
During the training phases, users of EXAKT will learn what the models are
intended to achieve and therefore how to measure their effectiveness.
It is important to understand that an EXAKT model is not usually used to
classify equipment into “good” and “bad” states. The optimal decision
output provides the optimal time at which to do maintenance given the
data used to the produce the model, current data readings, and
information about the relative cost of performing preventive maintenance
versus allowing equipment to fail.
An optimal decision requires a tradeoff between unnecessary preventive
work and missed failures. If a failure is ten times as expensive as
preventive work, one would expect to make some unnecessary preventive
removals. If a failure is only twice as expensive, some failures should be
allowed to occur. These occurrences are not shortcomings of EXAKT and
its models.
The way to determine if an EXAKT model is effective is to determine how
well it actually fits the data. There are techniques to assess model fit
during the modeling phase itself. In the long term, the following steps
should take place periodically to monitor the ongoing performance of the
models:
- Assess how the model behaves on the data used to produce the
model. How many failures occurred? How many preventive removals
occurred? How much useful life does each asset enjoy? This
establishes a benchmark.
- onitor the performance of the model as data are collected and more
failures and/or preventive removals occur. Are failures and removals
occurring at the same rate? Is a similar amount of useful life being
enjoyed? Are predictions of remaining useful life accurate over the
short term?
How BANAK can Support an Organization’s Objectives
A Typical Implementation
Site visit by a BANAK consultant to collaborate with a company’s
condition monitoring staff and maintenance engineers to establish data
acquisition protocols and the transfer of data electronically to BANAK in
Toronto, and to discuss the content and meaning of the data contained
in the condition monitoring databases and CMMS systems. (Typically 2
days travel + 4 days at site)
Analysis of condition monitoring and CMMS data for a selection of
equipment:
5-20 days in Toronto depending on data quality and number of
equipments being analyzed.
Site visit to: Present to company’s condition monitoring engineers the
results of the equipment analysis including identification of any measurements that are highly correlated with different failure modes
(Typically 2 days travel + 4 days at site).
Expected Duration of Assignment (First Phase)
A typical estimate of consulting days for this work is: 17 - 32.
Deliverables to Client
- EXAKT model development as described in “A Typical
Implementation” above: 17 – 32 days.
- EXAKTd for Company: cost USD 35,000 for one license or USD 50,000 for up to five users.
- Training for EXAKTd: 2 days.
- EXAKTm for Company: cost USD 50,000 for one license
- Training for EXAKTm for routine model updates: 1 day.
- If the result of the assignment is considered successful by a
company then BANAK shall provide a second proposal for the
implementation of EXAKTm + training + advisory in the
development of the data cleaning and modeling for other CM
techniques.
A Closing Suggestion
Thank you for your interest in EXAKT. We trust this brief coverage
will have provided much of the information you were looking for.
We understand that your decision to adopt EXAKT is an important one
in several respects. The commitment is substantial in terms of time,
money and effort. That’s why we would be most pleased to answer
any and all additional questions you may have, personally, by
telephone.
Please call us at your convenience. If we’re not reachable at that time
we will call you back. We want to ensure that you are totally
conversant with all aspects of your EXAKT adoption. Call me at
Canada Code 1, 416 234 8558. Or e-mail me at
jardine@mie.utoronto.ca
Andrew Jardine
|